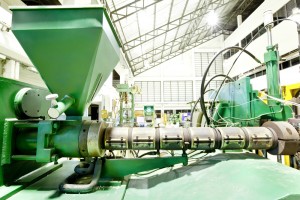
From staplers to office chairs, car bumpers to airplane seats, and tableware to cargo containers, humans have found an incredible number of uses for plastic. How do all these thousands, millions and billions of plastic products get made? Historically, just four — and more recently, five — straightforward processing methods have allowed us to create the myriad of plastic products we all rely on in our day-to-day lives.
Three ways to mold
Long before polymer pioneers figured out how to turn oil and natural gas into plastic, artisans and toolmakers were using the process of molding to create. Three molding methods are commonly used in processing plastics:
- Injection molding employs plastic pellets or granules. The particles feed from a hopper into a heating chamber, where the heat and mechanical manipulation melt the solid material into a liquid form. High pressure then forces the fluid out of the heating chamber and into a cool, closed mold. Inside the mold, the plastic cools and hardens until it again becomes solid. When the mold is opened, viola! The finished part can be removed. Many disposable plastic containers used in food packaging are made through injection molding.
- Heat also plays a role in rotational molding. Plastic granules get placed inside a closed mold that’s mounted on a rotational machine that can spin the mold on two axes simultaneously. The mold gets heated to melt the plastic, and the rotation spreads the liquefied plastic until it uniformly coats the inside of the mold. When the mold cools, the rotational molding produces hollow products, such as large toy balls and fuel tanks.
- The third molding process, blow molding, is usually done in tandem with extrusion or injection molding. In extrusion blow molding, semi-molten thermoplastic is formed into a tube, a chilled mold is clamped around the tube, and then compressed air, forced through the tube, helps it conform to the interior of the mold. Milk bottles and commercial drums are made through blow molding. In a process that combines injection and blow-molding techniques, injection molding is used to create a preform, which is then heated to soften it and finally blown into a chilled mold to create the final shape. Soft-drink bottles are typically made this way.
Traditional and cutting edge
Again starting from plastic pellets or granules, extrusion feeds the pellets from a hopper into a long, heated chamber. A continuously revolving screw moves the material through the chamber, and the plastic melts under the heat and mechanical force. The screw forces the liquid plastic out of the chamber through a small opening or die to create the shape of the final product. As it leaves the die, water or air is used to cool the material and finish the product. Extrusion is the main processing method for plastic films and bags.
A form of extrusion plays a role in the most modern plastics processing method: 3D printing. While 3D printing can be done with other materials, the majority of home printers use plastic to create a wide range of finished products. In fused filament fabrication — the most common type of home 3D printing — a 3D printer moves thermoplastic fibers from a holding compartment into an extruder[1]. A hot end melts the plastic into a liquid form, and the printer, using information provided by a 3D computer model, builds the product by adding layer upon layer of plastic. Anyone who remembers old dot matrix printers can envision the basics of how the layering process works.
Of course, there are many other ways to process plastic into the products we use every day, and the technology of 3D printing is ever-evolving. Who can predict what the next advance in plastic processing will be?
[1] https://3dprint.com/82272/what-3d-printing-works/