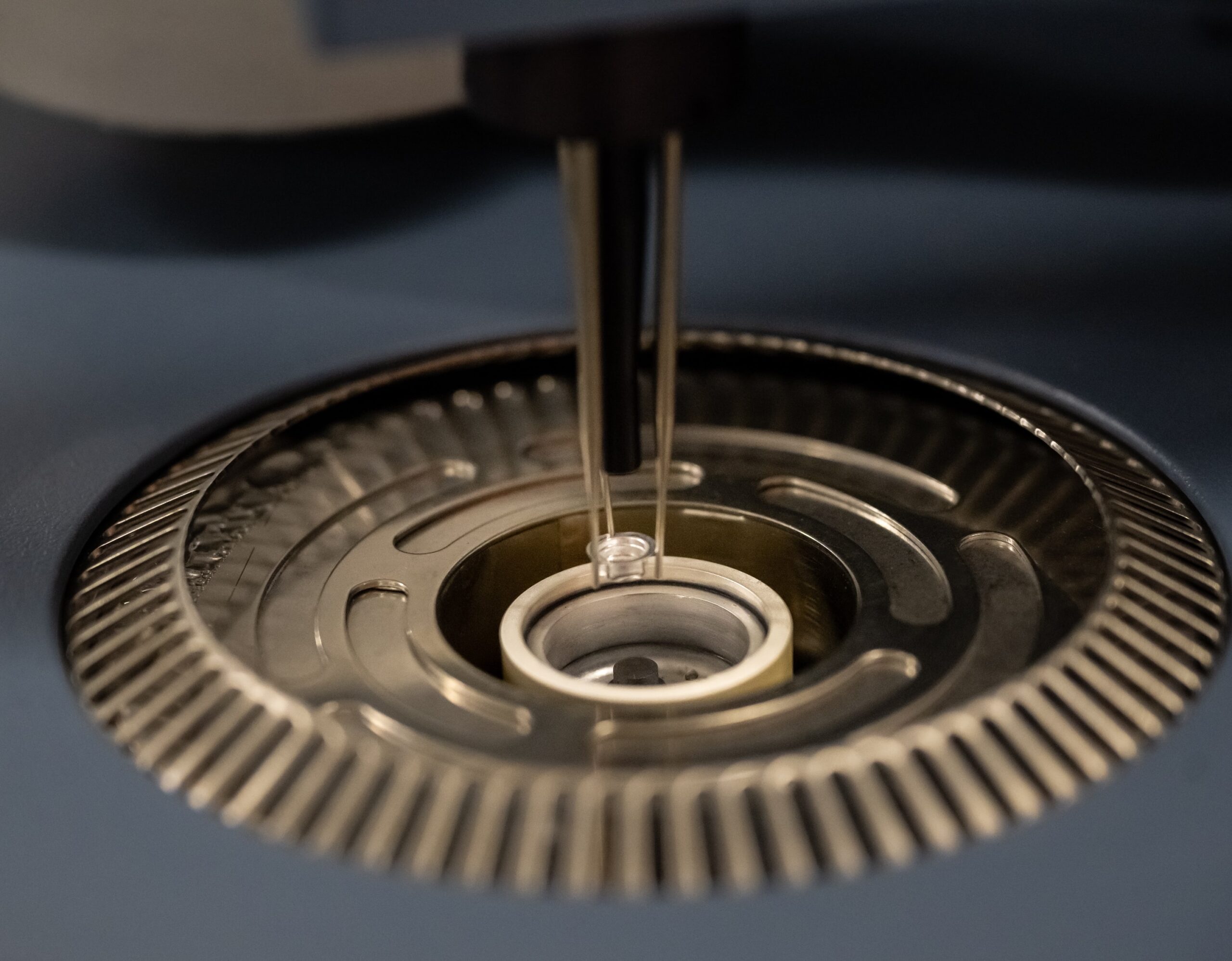
Thermal
Melt Flow Rate is an analysis method that determines the ease of flow of plastic materials.
Melt flow rate depends on molecular weight, additives, and other ingredients. The melt flow rate value allows for direct comparison of materials to each other and is a valuable tool for quality assurance.
Approaches
The sample must be “meltable” in order to be evaluated using the MFI instrument. To charge the instrument with the sample, the sample has to have a particle size that is on the order of about 3-mm or less so that it can be loaded into the barrel portion of the instrument. So, typical plastic pellets are an appropriate particle size. The measurement involves weighing the mass of a plastic that flows from the instrument over a timed interval. Some polymer materials (polyethylene for bag applications) have such high flow rates that the MFI method in that case must be an automated system to obtain reliable results.
Thermoplastic materials can be evaluated using the MFI method of analysis. As well as Melt Flow Rate (MFR) and Melt Volume Rate (MVR) Some examples of materials that are evaluated include:
- Polypropylene
- Polyethylene
- Polyamide (nylon)
- Polystyrene
- Polycarbonate
- Polyester
- Other Polyolefins
ASTM D1238 – Procedures A & B
ISO 1133-1
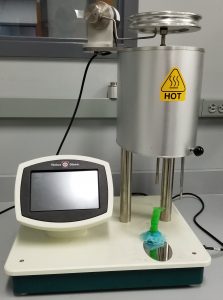
Sample Considerations
An MFI sample must be capable of being melted. A single MFI determination requires about 10 grams of material, and samples are typically evaluated in duplicate. Usually a few trial runs are needed to set the proper mass charge for the tester, so ideally we like to have about 100 grams of sample. Typically samples are in the form of:
- Pellets
- Sheets
- Powders
- Finished Products*
*Because we can convert manufactured products into plastic powder, the melt flow analysis can be reliably determined for finished products.
Contact us to talk through your specific sample considerations.
Experience
Work we’ve done with Melt Flow Rate includes:
- Raw material certification
- Comparison of “good” and “bad” samples
- Batch to batch comparisons
- Grade differentiation of materials
- Determination of the nature of material degradation (processing, transportation, storage, and drying conditions)